Pegboard Baskets & Quality Control: Evaluating Excellence with Common Metrics
Quality Assessment with Pegboard Baskets: Organize products or services using pegboard baskets for e…….
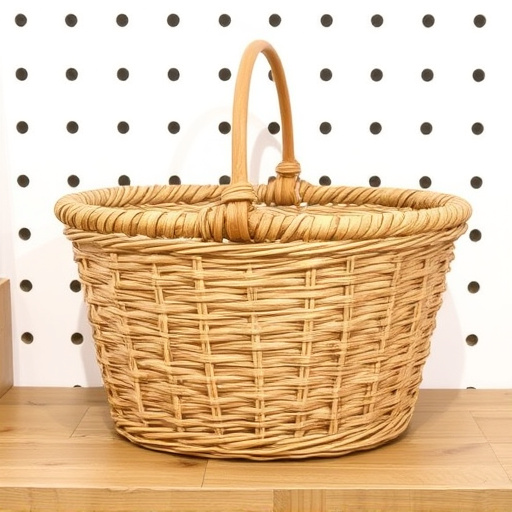
Quality Assessment with Pegboard Baskets: Organize products or services using pegboard baskets for efficient evaluation based on defined criteria, crucial for maintaining industry standards and exceeding customer expectations. This structured approach identifies strengths, weaknesses, and improvement areas through data-driven decisions, optimizing processes, and continuously enhancing offerings. In complex industries like manufacturing and retail, blending key metrics and techniques ensures product quality, with tools like pegboard baskets tested for material strength, shelf life, and load capacity using SPC and Six Sigma methods. Best practices include regular audits, feedback loops, open communication, and KPI sharing to foster continuous quality improvement and employee engagement.
Quality assessment is a critical process that ensures products meet high standards. This article delves into the essential aspects of quality control, guiding businesses towards excellence. We explore fundamental concepts, starting with ‘Understanding Quality Assessment’, and delve into innovative practices like using pegboard baskets for efficient quality control.
Key topics cover implementing frameworks, choosing metrics, and best practices for continuous improvement, all vital for success in today’s competitive market. Discover how these strategies can transform your quality management approach, especially leveraging pegboard baskets as a practical tool.
- Understanding Quality Assessment: A Fundamental Concept
- The Role of Pegboard Baskets in Quality Control
- Implementing a Comprehensive Quality Assessment Framework
- Common Metrics and Techniques for Evaluating Quality
- Best Practices for Continuous Quality Improvement
Understanding Quality Assessment: A Fundamental Concept
Quality assessment is a critical process that involves evaluating and measuring the performance, effectiveness, and overall quality of products or services. It’s akin to using pegboard baskets to meticulously sort and organize items based on specific criteria. This concept serves as a cornerstone in various industries, ensuring that standards are met and customer expectations are consistently exceeded.
By implementing robust quality assessment methods, businesses can identify strengths, weaknesses, and areas for improvement within their operations. It allows for data-driven decisions, process optimization, and the continuous enhancement of offerings. Much like arranging items in pegboard baskets according to size, shape, or function, quality assessment organizes aspects of a product or service, leading to better management, efficiency, and satisfaction.
The Role of Pegboard Baskets in Quality Control
In quality assessment, pegboard baskets play a pivotal role in organizing and streamlining various control processes. These versatile storage solutions allow for efficient sorting, grouping, and tracking of products or inspection items, enhancing overall productivity during quality control checks. With their customizable design, workers can quickly access and retrieve standard-sized components, ensuring a seamless workflow.
Pegboard baskets facilitate a structured approach to quality control by providing dedicated spaces for different product categories or inspection stages. This organization reduces the risk of errors and improves the accuracy of assessments. Moreover, their lightweight yet durable construction enables easy movement across work stations, promoting a dynamic and responsive quality assurance environment.
Implementing a Comprehensive Quality Assessment Framework
Implementing a comprehensive quality assessment framework is akin to organizing your workspace with pegboard baskets—each labeled and designed for a specific purpose. In this approach, every aspect of a process or project is meticulously evaluated, ensuring nothing is left to chance. It involves setting clear standards, defining measurable criteria, and establishing robust systems for regular review and feedback. This structured method enables organizations to identify strengths, pinpoint areas for improvement, and make data-driven decisions.
Just as pegboard baskets facilitate easy access and efficient organization, a well-structured quality assessment framework streamlines operations. It promotes consistency, enhances productivity, and fosters a culture of continuous improvement. By regularly assessing and refining processes, teams can adapt to changing demands, deliver higher-quality outputs, and ultimately drive business success.
Common Metrics and Techniques for Evaluating Quality
When assessing quality, especially in complex fields like manufacturing and retail, several key metrics and techniques come into play. For instance, evaluating product quality involves examining attributes such as durability, functionality, and aesthetics—all of which can be quantified through standardized tests. In the case of pegboard baskets, for example, measures like material strength, shelf life, and load-bearing capacity are crucial. These physical properties directly impact the basket’s utility and longevity in various environments.
Additionally, techniques such as statistical process control (SPC) and Six Sigma are employed to analyze data and identify variations. SPC involves monitoring processes in real-time to ensure they meet quality standards, while Six Sigma focuses on reducing defects by pinpointing and eliminating root causes. In a dynamic market where consumers demand consistent excellence, these methods enable businesses to adapt quickly, ensuring products like pegboard baskets maintain high standards across batches and production runs.
Best Practices for Continuous Quality Improvement
In the quest for continuous quality improvement, adopting best practices is paramount. One effective strategy involves implementing a system of regular audits and feedback loops. This can be facilitated through tools like pegboard baskets, which organize and categorize feedback from various sources, ensuring no valuable input goes unnoticed. By centralizing and categorizing feedback, teams can quickly identify recurring themes and areas for enhancement.
Additionally, fostering a culture of open communication encourages employees at all levels to actively participate in the quality assessment process. Management should promote transparency by sharing key performance indicators (KPIs) and inviting suggestions from staff members who interact directly with products or services. This collaborative approach not only enhances overall quality but also boosts employee engagement and ownership.
In conclusion, quality assessment is an indispensable process that ensures excellence across various industries. From understanding foundational concepts to implementing robust frameworks and utilizing advanced metrics, each step plays a pivotal role in achieving optimal results. Integrating tools like pegboard baskets into quality control measures demonstrates the practical application of these principles. By embracing best practices for continuous improvement, organizations can sustain their competitive edge, enhance customer satisfaction, and foster an environment that values craftsmanship and precision.